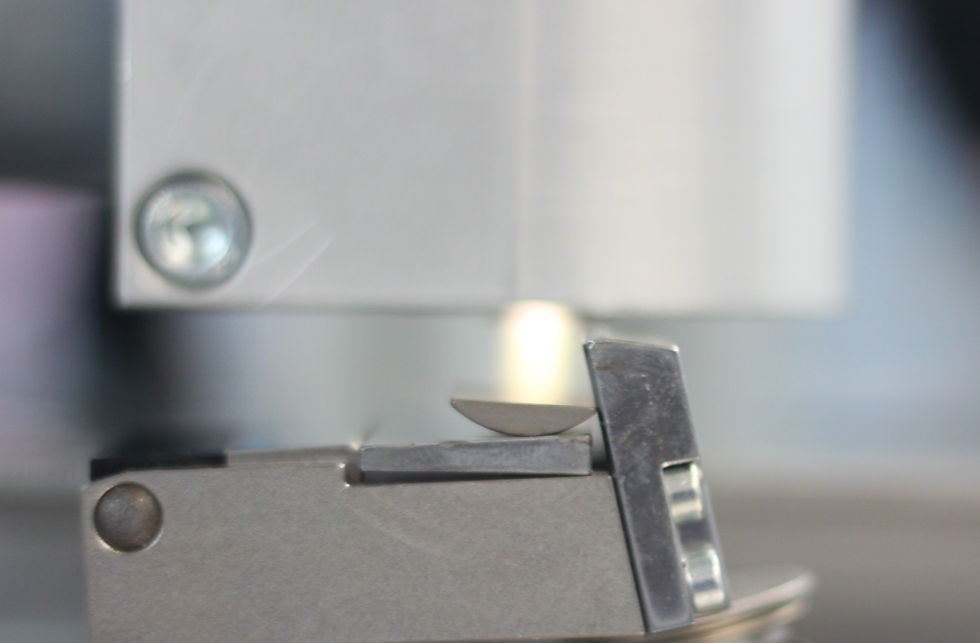
safe in motion
between north- & southpole
fully automatic permanent magnet motor assembly
electric motors
assembly of haprotec
the highly flexible automation solution
process stability
reduced costs
high flexibility
easy expandability
improved product quality
Expanded design freedom
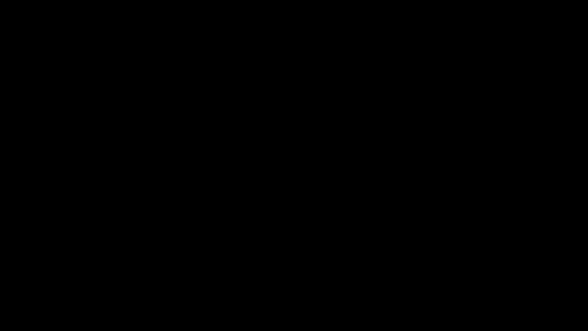
The production of permanent magnet motors places high demands on precision and efficiency. Traditionally, magnets are only magnetised after they have been placed on the rotor, which is associated with various challenges. haprotec GmbH has developed an innovative and patented process that enables already magnetised magnets to be mounted on rotors fully automatically. This process utilises the existing magnetic force and works with it instead of against it, which offers numerous advantages for motor production.
Challenges of conventional processes
In conventional production systems, magnets are only magnetised after they have been placed on the rotor. This procedure has several disadvantages:
- High process costs: Costs increase, especially with a large variety of products, as investments have to be made for different magnetisation tools.
- Limited flexibility: Variations in pole pitch are limited by the magnetisation tools available, which restricts the ability to adapt to different designs.
- Difficult magnetisation: Small, closely spaced magnets pose a challenge as their magnetisation can be complex and error-prone.
- Design limitations: Magnet carriers must be designed to positively hold the magnets in place, which reduces the scope for innovative designs.
The innovative process from haprotec
To overcome these challenges, haprotec has developed a process that automates the assembly of already magnetised magnets. The magnetic force is used specifically to support the process. This leads to a number of advantages:
- Increased process stability and reduced costs: by outsourcing the magnetisation process, production costs can be reduced and the stability of the overall process increased.
- High flexibility: The system enables the cost-efficient production of a wide range of motor variants on a single platform.
- Easy expandability: New motor models can be integrated into the existing production without great effort, which saves investment costs.
- Improved product quality: A gentle gripping and setting process minimises damage to the magnets and increases the service life of the end products.
- Extended design freedom: Thanks to flexible pole pitches and the secure fixing of the magnets without external holders, developers can design more creative and efficient magnet carriers.
Automated assembly process
The entire assembly process is fully automated and comprises several precisely coordinated steps:
1. plasma cleaning: The magnets are first subjected to plasma cleaning to remove impurities and ensure optimum adhesion.
2. adhesive application: The adhesive is then applied in precise doses to ensure a firm and permanent bond between the magnet and rotor.
3. optical inspection: The applied adhesive track is checked using optical systems to ensure that the adhesive has been applied evenly and in the correct quantity.
4. magnet placement: Finally, the magnets are precisely positioned and fixed on the rotor.
Optionally, data on process and system statuses can be recorded, visualised and forwarded to higher-level MES or trace systems throughout the entire process to ensure seamless documentation and quality assurance.
Customisable system concepts
haprotec offers various machine models for permanent magnet assembly, including
- XTS high-speed system: This system is characterised by its high flexibility and expandability, making it ideal for production environments with frequently changing requirements.
- Classic rotary indexing version: This variant is particularly space-efficient and is suitable for production facilities with limited space.
Depending on requirements, the machines can be integrated into existing production lines as a stand-alone solution or as an inline variant. The customised fixtures for rotors and magnets allow flexible adaptation to different product variants. Depending on requirements, these holders can be changed manually or fully automatically.
Test laboratory for feasibility analyses
To ensure that the process is optimised to meet the customer's specific requirements, haprotec has its own in-house test laboratory. Here, tests can be carried out with the customised magnets as part of an initial feasibility analysis. Customers are invited to carry out appropriate tests on site together with haprotec's application experts. Alternatively, samples can be sent in for testing in the laboratory. These practical tests ensure that the developed solutions meet the high quality standards and function reliably in the real production environment.
With this innovative approach, haprotec is revolutionising the production of permanent magnet motors and offering companies an efficient, flexible and high-quality solution to the challenges of modern motor production.
haprotec assembly- & test laboratory

Our in-house laboratory allows us to test the setting of your magnets as part of the first feasibility analysis. We invite you to carry out individual tests with our application engineers.
Alternatively, you can also send us your individual samples and we will carry out the tests for you.